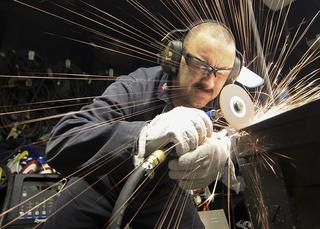
Normal Grinding Wheel
A normal grinding wheel has a support body made of steel with a central coupling region for the connection of the grinding wheel on a rotational drive. The carrier body has a peripheral surface on which an abrasive coating is applied. In the grinding operation, grinding wheel causes a deafening noise, so the use of a hearing protection is required. The reason for the noise is those vibrations generated during grinding operation. Vibrations transmit on all areas of the grinding wheel and also on the work-piece being machined. Because of the vibrations, the accuracy and the quality of the milling result may be adversely affected.
Copyright: Tyrolit (image link)
Research by Tyrolit
Tryrolit is one of the leading companies in the abrasives, it is based in Austria. In 2016, they thought of solving this problem with innovative design of the grinding wheel.
The new grinding wheel has two parts, a total support body is made of these two parts. The first part consists of an essential steel portion which is vibration and thermally conductive. The first part has a circumferential surface, on which an abrasive coating is sintered. A width of abrasive coating is approximately 5 mm. In general, in grinding process, the resulting vibration and heat can be discharged via the first part. If one were to use only a single-piece carrier body consisting entirely of a vibration-damping material, there would be an accumulation of heat that promotes vibration and wafer warp.
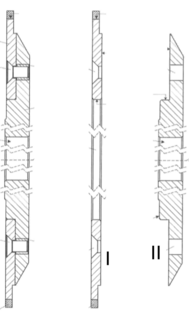
The first part is connected with the second part via two contact surfaces(One is around the drive axis other is in plane normal to the drive axis). The second part is in connection with the rotational drive shaft. The vibrations are transferred from the first part to the second part through those two contact surfaces. The second part made of a vibration-damping material. For example, damping can be done with cast iron with lamellar graphite or fiber-reinforced aluminum/bronze, carbon fiber reinforced plastic also can be preferred. Due to the vibration-damping properties of the second part, vibrations forwarded by the first part are effectively damped.
Assembly and Replacements
The second part has a coupling portion for connection the grinding wheel to a rotary drive. The coupling portion is nothing but a central bore. The coupling portion is continuously made in the vibration absorbing material of the second part. The second part acts as a hub. In this assembly of the grinding wheel, the first part is inserted on the second part. Second part has a cylindrical projection to accommodate the first part, this way the parts lie flush with one another.
Subsequently, the two parts are firmly connected together by screw connections with glued threaded bushes. When the abrasive layer arranged on the first part is fully consumed by the grinding operations, the first part can be removed and replaced by a new first part. The second part can be reused as long as it serves the purpose of vibration damping.
Key Advantages
The vibration damping by the second part of the support body is done in two directions: firstly vibrations generated by the abrasive coating and on the other hand vibrations from the the rotary drive. These two vibrations generating from two different sources are decoupled, if not then, additional strengthening of these oscillations take place and it is harmful. A damping of the vibrations saves the bearing of the spindle of the drive from early failure as it is less stressed.
Competition In Research
Robert Bosch GMbH(2007), Sankyo Diamond(2012), Taiho Diamond kogyo(2005) and Bando Kiko(2002). It’s very difficult to rule this technology for Tyrolit alone, as there are many similar designs being developed by the competition. Read more on Mechanical Engineering.